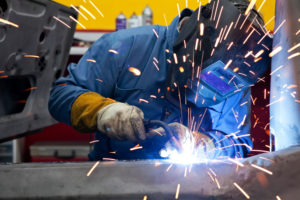
Welding on an automobile
Welding is a job that is performed in a variety of settings and in many different industries. One of the oldest and most important forms of welding has existed in the automotive industry. It is a common practice to weld together car parts, although this should not be attempted by anyone who is not a trained professional. This job takes years of practice to master and continues to be a valuable service in the auto repair industry. There is always a need for some kind of welding in auto restoration or auto body repair. This can create a comfortable living as skilled auto welders are a valuable commodity. Getting started on a career as an auto welder can begin today with an introduction to the training it will take to become a skilled professional.
Auto Welder Job Duties
The job of an auto welder may seem rather straightforward, although there are a lot of small details involved in these day-to-day activities. An auto welder will use specific techniques and tools for each individual job. Here is a look at some of the job duties that consume the everyday assignments of an automotive welder:
Performing these duties leads to the development of a specific set of skills. Auto welders carry out more than just the act of welding. They also maintain performance standards that are integral to the industry. Here is a look at some of the characteristics of an accomplished auto welder.
Time Management skills
Auto welders are capable of successfully planning out their daily work schedule. This includes approximate estimations of how long certain welding jobs will take.
Interpersonal skills
Welders interact with fellow workers and customers. There is a need for effective communication as it creates a better work environment and larger client base.
Decision Making
Auto welders rely on logic and a sound understanding of welding fundamentals to make necessary repairs. This includes a detailed analysis and evaluation.
Math and computer skills
There are basic computer fundamentals used by welders, in addition to mathematical concepts. This helps when making calculations before and during a welding project.
Problem Solving
Not every welding project is going to go as planned. It may take some quick thinking in order to make sure everything meets the exact specifications. Auto welders need to be able to think on their feet.
Auto welders have played an integral role in the automotive industry for generations. Technology is beginning to change the industry and some welders operate robots during the welding process. The human element still remains at the heart of auto welding and using technology to make this job more proficient has enhanced the overall skillset of auto welders.
Auto Welder Education
There are a number of technical components that auto welders need to follow throughout the welding process. That requires a formal education in which welders learn proper techniques. Those going through an auto welding education program are provided with the opportunity to practice and perfect those techniques. This involves classroom learning in addition to practicing in an actual workshop setting.
These programs are available through various community colleges, automotive institutes, technical colleges and vocational schools. These programs last anywhere from 6 to 9 months and conclude with the awarding of a certificate of completion. There is coursework involved and that is coupled with a hands-on portion in which students get to conduct actual welding of their own. Students who attend an auto welding program learn about the following topics:
In the auto welding industry, there is often the question of whether TIG or MIG welding should be used. TIG welding has its advantages as it leaves a softer seam while using less amperage and only a small bit of body filler to smooth out the surface. TIG welding is recommended when joining together a couple of smaller pieces of metal. TIG welding is also does not require as much maintenance.
MIG welding may not be the most popular choice of the two, although it still has its advantages. MIG welding is the more preferred option when it comes to larger and denser metal pieces. This is more of a heavy-duty tactic, and both MIG and TIG welding are primary parts of an auto welding education program.
Auto Welder Work Experience
Experience is an excellent teacher when it comes to auto welding. Educational training programs provide auto welders with plenty of practice and that allows them to enter into the workforce with confidence. There is a high priority on auto welding as it maintains the structural integrity of vehicles. Improperly welded vehicles can jeopardize everyone inside the vehicle and make it very unsafe for driving.
Work experience is needed to successfully pass a certification exam. Experience is also valuable when conducting job searches. This is why it is important for auto welders to accumulate as much work experience as possible.
Auto Welder Certification
The American Welding Society (AWS) offers several examinations to certify welders. There are different certifications, although auto welders can utilize the certification that applies to welders in general. This certification is known as a certified welder. The more experienced an auto welder becomes, the more he/she may consider earning multiple certifications. Here is a list of the welding certifications offered by the ASW.
The certified welder examination given by the AWS is performance based. There is no written portion of the exam. It essentially consists of one’s ability to perform various welds. There are also no prerequisite courses in order to earn a certification. Many training programs provide welders with the experience and skills needed to pass this certification exam. Welding skills are exhibited through by demonstrating fit-ups, positioning and assembly.
The AWS certification tests are administered at accredited test facilities. A failing score does not require any specific wait time to retake the test. Once a certification is earned, it can be maintained by submitting a certification maintenance form once every six months. There is a 60-day grace period for submitting these forms in the event that it has lapsed.
Earning a certification provides welders with a higher level of credibility and this can hold tremendous weight when applying for a job. Many businesses that offer auto welding will advertise the fact that their welders are AWS certified. This can be a major selling point when marketing to new clients. Industry certifications make customers feel more at ease. They also establish trust among customers and that can quickly help word of mouth business.
Automotive Welder Salary and Job Outlook
The U.S Bureau of Labor Statistics has grouped welders in with other technicians, which include cutters, solderers and brazers. Annual salary averages of the compiled data for this group stands at $42,450. The top 10% of this group average a yearly salary of $62,100, which comes out to $29.85 per hour. Automotive welders comprise roughly eighteen percent of this particular group. It is often difficult to pinpoint exact salary averages because of the lack of documentation among different welding jobs. For example, automotive welders have more of a presence in certain parts of the country. Yet, many data reports still label welders into one category, without identifying the individual specialty.
The states with the highest pay rates for welders differ in the sense that they are spread out all over the country. Here is a closer look at the top five paying states for welders, per the Bureau of Labor Statistics.
Welders who specialize in working on automobiles have the opportunity to make a comfortable living. It is a specialty skill that is of great importance in the auto industry. By the year 2024, there is expected to be a 4% increase in the number of welding jobs in the United States. Some states have higher growth rates than others. Texas has, by far, the most job openings for welders on a yearly basis and that is followed up by the states of California and Idaho, as both are almost similar when it comes to projected job openings over the next six years. Indiana and Pennsylvania are next up with a fourth and fifth ranking in that category.